
おしらせ&コラム
2024.12.25
製造現場でのリスクアセスメントの進め方とは?考え方や課題を解説
労働災害が起こりやすい製造現場において、危険性を洗い出すリスクアセスメントは大事な施策の1つです。
リスクアセスメントで危険性をはっきりと示すことで、いかにリスクを下げられるかを考えられます。
本項目では、以下の内容をまとめました。
・製造現場におけるリスクアセスメントの基本的な考え方
・製造現場でリスクアセスメントを実施する事業所の割合
・製造現場でのリスクアセスメントの実施プロセス
・製造現場におけるリスクアセスメント成功のためのポイントと課題
ぜひ最後までご覧ください。
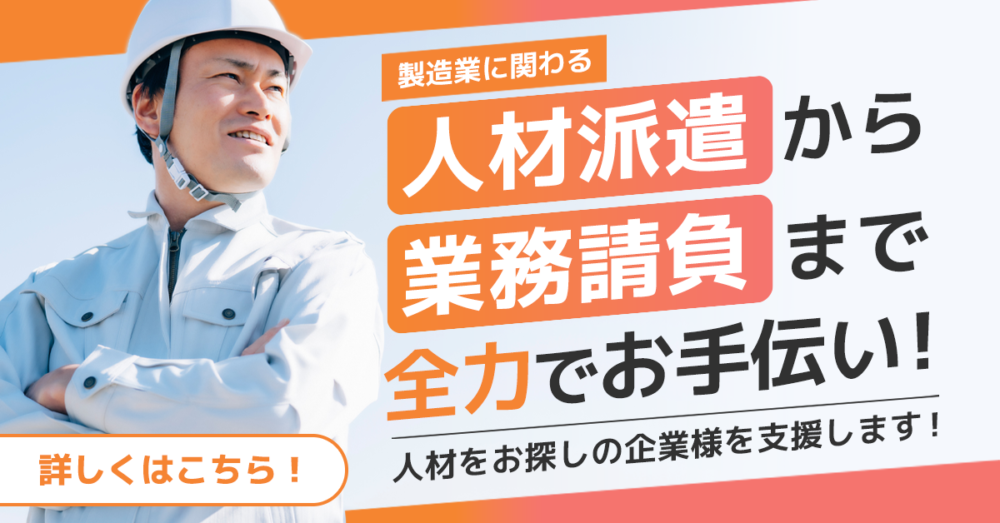
製造現場におけるリスクアセスメントの基本的な考え方
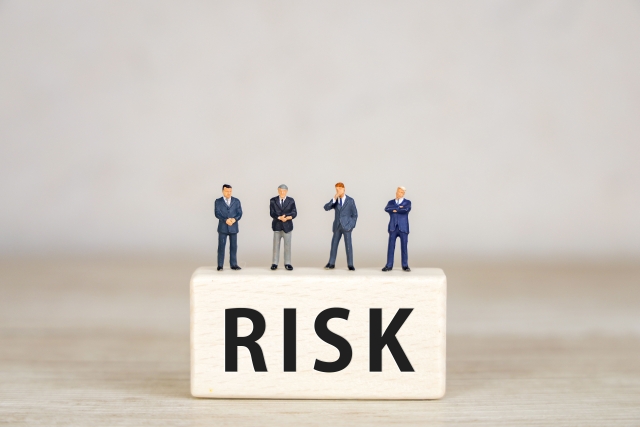
リスクアセスメントは、職場に潜む危険を特定し、それによる影響の度合いや発生の可能性を評価するプロセスを指します。
正しく実施することで、安全性向上だけでなく、生産効率の改善やコスト削減といった効果も期待できます。
本項目では、製造現場におけるリスクアセスメントの基本的な考え方についてまとめました。
そもそもリスクアセスメントとは何か
リスクアセスメントとは、業務上発生しうるリスクを特定し、それを分析・評価して適切な対策を講じることを目的とする安全管理の手法を指します。
特に製造現場では、作業手順や設備の安全性を見直し、リスクを考慮して事故やトラブルを未然に防ぐ対策が求められます。
製造現場にはさまざまな危険性が潜んでおり、いかに予防できるかが重要です。
その危険性をリスクアセスメントを通じて見積もった上で優先順位をつけてリスクを減らす対策を講じることにより、労働災害を防いでいくことが可能です。
ちなみに、リスクアセスメントは労働安全衛生法において努力義務とされている一方、安全データシート(SDS)交付が義務づけられている640の化学物質を取り扱う場合はリスクアセスメントが義務となっています。
製造現場におけるリスクアセスメントの必要性
製造現場では、製造物によって高温、重量物、化学物質など、さまざまな危険性・有害性が存在します。
これらのリスクをそのまま放置してしまうと、労働災害だけでなく製造物の品質に関する問題なども生じる可能性があるのです。
リスクアセスメントを行うことで、これらの諸問題を解消するほか、従業員の安全意識を高める機会にもつなげられます。
適切なリスクアセスメントを実施していくことは、組織全体の安全に対する考えを強化することにもつながります。
ただでさえ多い製造現場での労働災害の撲滅にも一役買う存在となるでしょう。
リスクアセスメントの導入による効果
リスクアセスメントの導入は、安全性の向上にとどまらず、さまざまな効果をもたらします。
まずは、事故やトラブルの減少により、労災コストや設備修理費を削減できます。
また、現場環境が改善されることにより、顧客からの評価にもつながりやすく、信頼性の高い企業イメージの構築につながるでしょう。
製造現場でリスクアセスメントを実施する事業所の割合
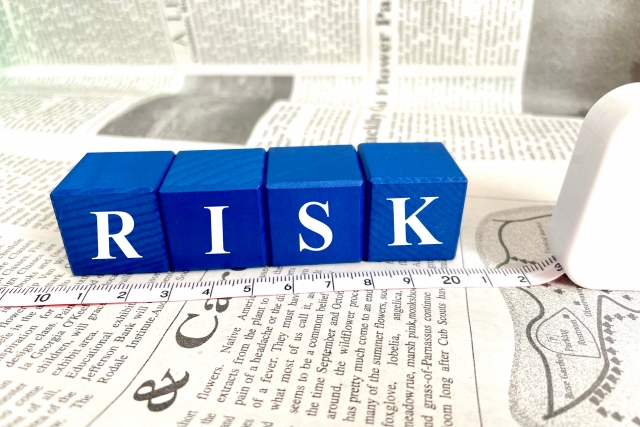
製造現場において実際にリスクアセスメントを実施している割合は、どれくらいなのか気になる方も多いはずです。
過去に行われた調査では、リスクアセスメントを実施していると答えた事業場は82.8%と多くの事業場が実施しています。
事業場の規模別でみても、多少のバラつきはあれど、規模に関係なくおおむね7~8割台の実施率をキープしている状況です。参照:中央労働災害防止協会「平成23年度リスクアセスメント/OSHMSへの取り組み状況等に関するアンケート調査結果」
建設現場においてもリスクアセスメントを行うケースは9割ほどあり、高所からの墜落や転落、建設機械の危険性などの項目でリスクアセスメントが頻繁に行われています。参照:厚生労働省「令和5年 労働安全衛生調査(実態調査) 結果の概況」
よくある危険に対してリスクアセスメントを行う企業が多いと言えるでしょう。
製造現場でのリスクアセスメントの実施プロセス
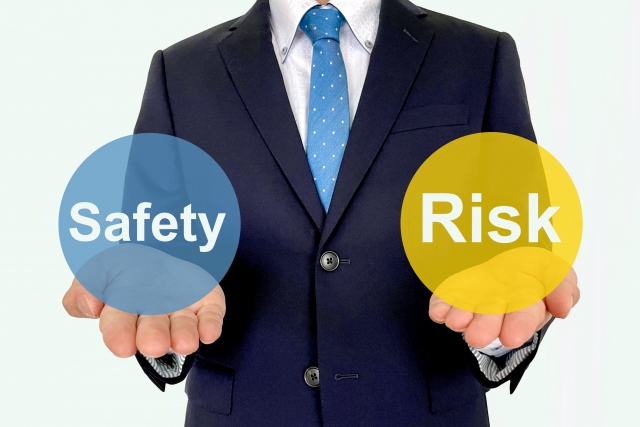
リスクアセスメントの成功は、計画的かつ段階的な実施によってもたらされます。
具体的には、リスクの特定や評価、優先順位の設定、対応策の実施、効果測定というプロセスが基本になります。
本項目ではこれらのプロセスについてまとめました。
リスクの特定と評価手法
製造現場におけるリスクを特定する際には、作業手順や設備の使用状況を詳細に調査する必要があります。
この際、ヒヤリハット報告や事故履歴を活用することが有効です。
また、製造現場におけるリスクの評価を行う際には、労働災害・事故の発生確率や影響度を数値化することで、具体的な優先順位を明確にします。
こうした取り組みにより、リスクを洗い出し、効果的な対策が立てられるようになるのです。
優先順位の設定と対応策の決定
製造現場におけるリスクが特定された後、それぞれのリスクに対して優先順位を設定します。
リスクアセスメントを行う中で、まずリスクの発生確率が高く、影響度が大きいものから順に対策を進めるのが基本となります。
例えば、リスクの発生確率が高いものがあれば、安全装置の導入や作業手順の変更を行うなどして、リスクを減らす施策を計画します。
計画を立てる中で、実行しやすい施策なのか、実行するにあたってコストがどれくらいなのかを考慮し、ベストな解決策を選択します。
リスク軽減策の実施と効果測定
リスクアセスメントによって、リスクの軽減策を検討したら、あとはその軽減策を実際に行っていく必要があります。
実際に実行して対策の効果を測定したら、当初の期待に見合う改善が得られるかをチェックします。
効果があるかどうかはすぐに出るものではなく、一定期間モニタリングが必要です。
モニタリングの結果、効果が持続的に出ればその軽減策を実行し続ければよく、出なければさらなる改善案を出して、再びモニタリングを行います。
製造現場におけるリスクアセスメント成功のためのポイントと課題
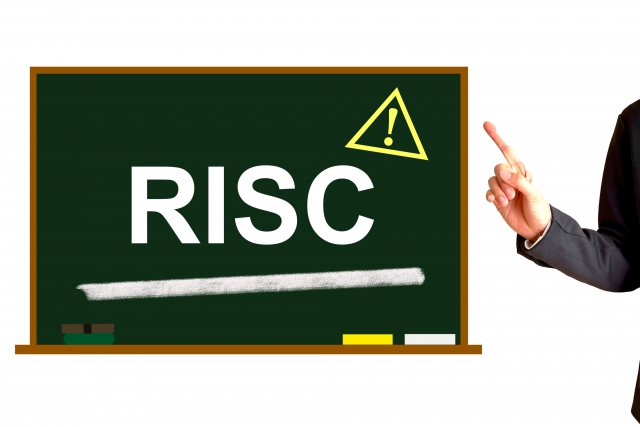
リスクアセスメントを成功させるには、全従業員の協力と継続的な取り組みが必要です。
また、実施に伴い、新たな課題を見つけて、柔軟に対応することも求められます。
本項目では、リスクアセスメント成功のポイントや課題をまとめました。
従業員の参加とコミュニケーションの重要性
リスクアセスメントは管理者だけでなく、現場の従業員が全員参加することが必須と言えます。
組織内での情報共有や意見交換を拠り所にすることで、全員が一体となって安全性向上に取り組むという姿勢につながります。
職場の従業員が全員参加することは危険に対する意識を強めるだけでなく、リスク軽減策を全員が把握して実行することに大きな意味を持つのです。
安全に対する強い意識を持ち、製造現場に安全文化を採り入れていくことでリスクを減らすことにつなげられます。
コミュニケーションを深めていき、危険性に対する共有を重ねていくことで、事故を未然に防げるようになるでしょう。
リスクアセスメントの定期的な見直しと更新の必要性
リスクアセスメントは一度実施すれば終わりではありません。
現場環境や作業内容が変化する中で、新たなリスクが発生する可能性があるためです。
変化が多い製造現場ほど、リスクアセスメントの定期的な見直しが求められます。
定期的な見直しを行い、軽減策を再度見つけ出し、安全対策を維持し続けることが重要です。
継続的な改善文化の構築
従業員によってはリスクアセスメントを作業として捉える人がいるかもしれません。
これを作業ではなく、組織の文化として定着させ、改善文化として昇華させることが大切です。
改善文化につなげていくには、トップマネジメントの継続や継続的な教育・訓練が必要です。
改善文化が作られれば、安全で効率的な職場運営が実現します。
そして、業務改善をはじめ、さまざまな改善活動につながっていくでしょう。
まとめ
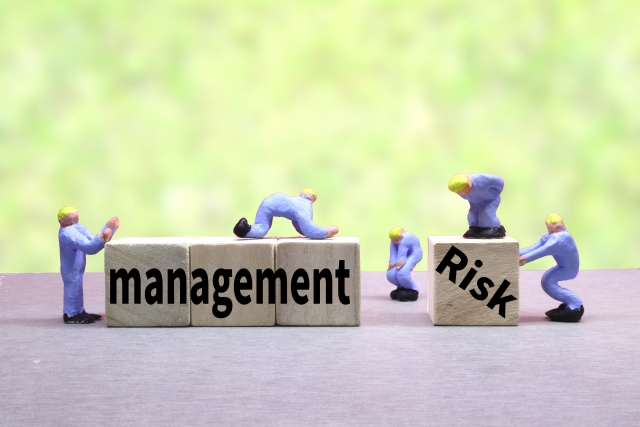
リスクアセスメントそのものは努力義務ですが、やっておいて損は1つもありません。
むしろ危険性のリスクがある製造現場では義務として行っておきたいものと言えるでしょう。
従業員に誇りをもって安心して働いてもらうためにも、リスクアセスメントは必要です。
Contact
お問い合わせ
ご相談・ご質問等ございましたら、
お気軽にお問い合わせください。
お問い合わせフォームはこちら
local_post_office お問い合わせ