
おしらせ&コラム
2024.12.13
製造業で業務改善を目指す道筋とは?3つのポイントを解説!
製造業において、業務改善を行うことは生産性向上を始め、さまざまな点において必要です。
あとは業務改善に向けてどのような道筋を辿るべきかですが、今回は3つのポイントを解説します。
本記事では、以下の内容をまとめました。
・製造業の業務改善の道筋その1現状分析と課題の特定
・製造業の業務改善の道筋その2生産効率の向上を目指す
・製造業の業務改善の道筋その3品質向上とコスト削減
ぜひ最後までご覧ください。
製造業の業務改善の道筋その1現状分析と課題の特定
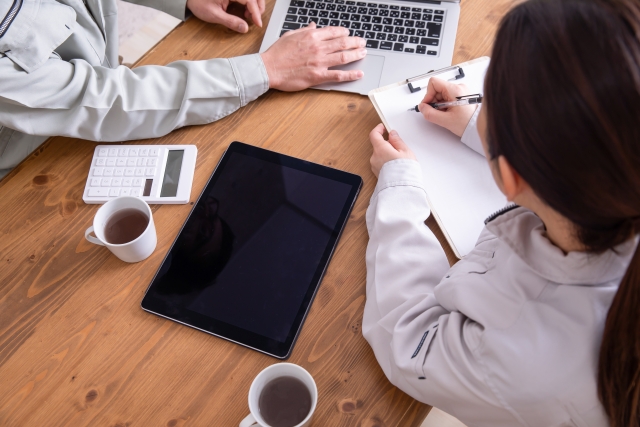
製造業における業務改善では、現状の課題を正確に把握することが重要です。
現場で何が起きているのか、どこに改善の余地があるのかをデータや作業の流れから分析することが求められます。
本項目では、現状分析・課題の特定などをまとめました。
現場データの収集と可視化
現場の業務改善を行うにあたり、第一歩となるのが、現場の実態に関してデータで捉えていくことです。
製造現場において、作業時間や生産量、エラー率などのデータを継続的に収集し、可視化することが必要です。
可視化させることで、現場で生じている無駄や非効率な生産工程が浮き彫りとなります。
最近ではIoT技術やセンサーが活用できるので、リアルタイムで現場の状況を把握することが可能です。
今までは見えなかった課題が早期に発見されるため、迅速に対応する体制を整えられます。
ボトルネックの特定
生産工程における無駄に関して、度々問題となるのがボトルネックです。
ボトルネックは、生産工程において遅延や不均衡を引き起こすため、生産効率を下げてしまう要因となります。
そのため、製造ラインの流れを阻害しているボトルネックを特定することにより、生産性の大幅な向上が可能となります。
特定にあたっては、ツールやフレームワークの活用によって、工程ごとの処理能力を分析し、改善の必要な箇所が明確化されるでしょう。
ボトルネックを特定する作業がしっかりと行われれば、ボトルネックの解消に向けた設備投資が行えるほか、効果的な資源配分や作業改善が可能になります。
作業標準化の見直し
業務改善に向けて不可欠な取り組みとして作業の標準化が挙げられます。
作業の標準化は、作業のやり方や手順を統一させることで、品質を一定の状態に保ち、効率化を図っていく方法です。
一方で、作業の標準化が進んでいない現場や昔のやり方が浸透して変えられない状況では、いきなり作業の標準化を目指しても効果は乏しいと言えます。
まずは現場の実態に即した標準化を目指すことが求められます。
作業手順をまとめるほか、作業標準化の完成に向けて基準の見直しなど進める様にしていくことが必要です。
製造業の業務改善の道筋その2生産効率の向上を目指す
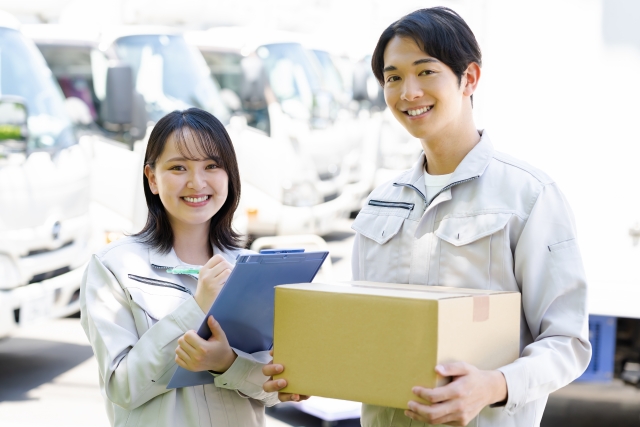
製造業で利益を増やしていくには、生産効率の向上は大前提であるとともに、競争力を高めていくのに避けては通れません。
そのため、自動化や作業工程の最適化などを行い、より少ないリソースで高品質な製品を迅速に提供する体制を構築することが求められます。
本項目では、生産効率の向上を目指す道筋などをまとめました。
自動化技術の導入と活用
生産効率の向上になくてはならないのが自動化の技術です。
自動化を行うことで、労働力不足の解消や生産性向上に大きく寄与します。
特に製造業は慢性的な人手不足に悩まされており、いかに人材を確保するかが問題視されています。
この状況では生産効率の向上以前に、生産状況を維持するのも大変と言えるでしょう。
自動化をするにあたり、ロボットやAIを活用することで、繰り返しの作業や精密な工程を効率化することが可能であり、人的ミスの削減も行えます。
特に、AIを活用した需要予測や工程の最適化は、生産計画の精度を高め、無駄を削減します。
一方で、自動化導入には設備投資や適切な教育が必要です。
スムーズな自動化に向けて、現場のニーズを考慮した計画的な実施が求められます。
レイアウト改善による作業動線の最適化
生産効率の向上につながる手法に、生産現場におけるレイアウトの改善があります。
例えば、動線が複雑な場合、本来カットできる移動や作業の手間が生じやすく、作業時間をいたずらに増やすほか、疲労にもつながるでしょう。
無駄な時間・疲労が生じることは、労働災害につながりやすいほか、ヒューマンエラーを誘発することにもつながります。
レイアウトの改善では、まず生産現場の状況をしっかりと観察するほか、さまざまなシミュレーションが欠かせません。
シミュレーションにあたっては、機械の配置や通路設計の見直しを行い、効率的な動線を構築します。
他にも5S活動(整理・整頓・清掃・清潔・しつけ)を併用していくことで、よりスムーズな作業環境が整います。
ジャストインタイムの導入
生産性の向上に必要なやり方に、「ジャストインタイム(JIT)」があります。
ジャストインタイムは、必要なものを必要なタイミングで生産することにより、在庫を削減するだけでなく、生産効率を高めることにもつながるという手法です。
無駄な在庫や過剰生産を防ぐことにより、リードタイムを短縮する効果があります。
ジャストインタイムを導入するには、関係各所の連携が求められるほか、取引先との情報共有や迅速な対応体制が欠かせません。
ジャストインタイムが成功すれば、フレキシブルでコスト効率の高い生産体制が構築されます。
製造業の業務改善の道筋その3品質向上とコスト削減
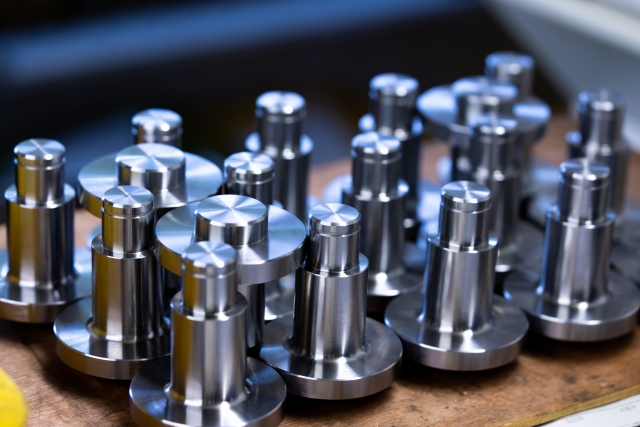
製造業の業務改善によって、品質向上やコスト削減を図ることができます。
高品質な製品を提供しつつコストを抑えることができれば利益の最大化も可能である一方、なかなか難しい問題でもあるのです。
本項目では、品質向上とコスト削減の道筋をまとめました。
QC活動の強化と社員教育
品質向上を目指すにあたり、重要となるのがQC(品質管理)活動です。
QC活動は現場における品質向上に不可欠な取り組みであり、定期的な改善活動を行うことによって、不良品の発生を防げます。
不良品の発生率が下がれば、顧客満足度にもつながるため、QC活動は行い続けて損がないものです。
一方で、QC活動を効果的に進めるためには、従業員の教育が重要と言えます。
従業員1人1人が品質に対する意識を高めていき、品質向上につながる必要なスキルを磨くことで、現場全体の意識改革が可能となります。
廃棄物の削減と資源の有効活用
生産工程の中で生じる廃棄物を少しでも削減することは、環境負荷の軽減はもちろん、コスト削減にも直結します。
工程で発生する廃棄物やその量を分析し、リサイクル可能な資材や代替材料の活用を進めていきます。
資源の有効活用を促進する動きは、結果として生産効率の向上にもつながるのです。
何より循環型経済を取り入れる企業姿勢は、顧客や社会からの信頼を得る要素にもなります。
メンテナンス管理の効率化
生産工程で用いられる設備の適切なメンテナンスは、ダウンタイムを防ぎ、生産性を維持する上で欠かせません。
事前にダウンタイムの予防保全や監視に力を入れることで、予期せぬトラブルを避けられます。
IoTセンサーやデータ分析などを活用したスマートメンテナンスによって、必要な箇所に最適なタイミングでメンテナンスを実施し、コストを抑えつつ効率を高めることが可能です。
まとめ
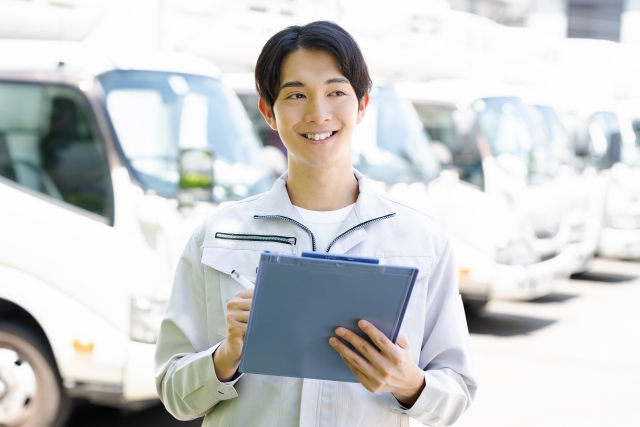
製造業の業務改善は生産性向上、利益の最大化など、さまざまなメリットがあります。
一方で、従業員の理解を得続けることも何より重要です。
なぜ業務改善を行い続けるのか、その意義をしっかりと伝え、メリットが非常に大きいことを実感してもらうことが大切です。
Contact
お問い合わせ
ご相談・ご質問等ございましたら、
お気軽にお問い合わせください。
お問い合わせフォームはこちら
local_post_office お問い合わせ